Characteristics of Switchgrass Lignin Extracted by Different Solvent Pretreatments
07/05/2022
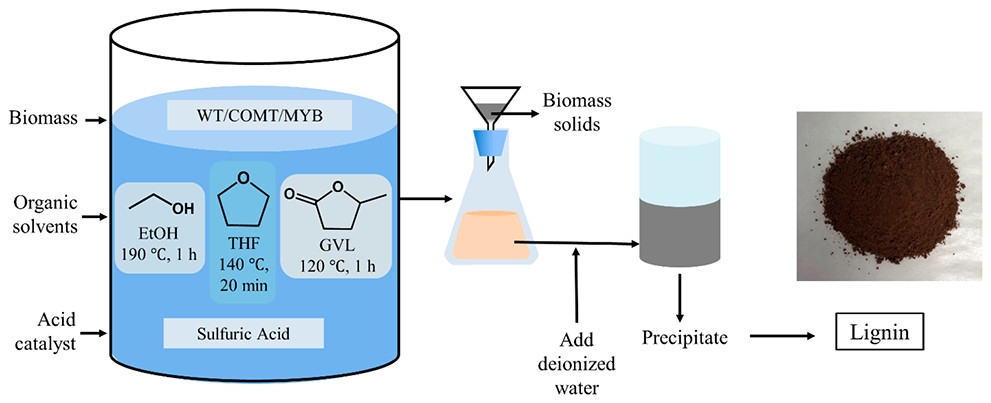
Scheme of switchgrass pretreatment. Switchgrass is pretreated in various organic solvents under moderately elevated temperature, pressure, and dilute acid (left image). The process extracts lignin (right image) from the cellulose, resulting in various lignin dimers and oligomers which are suitable for further processing and valorization.
The Summary
Biomass recalcitrance due to the complex hierarchical structure of plant cell walls presents a challenge in biorefinery systems which seek to maximize biomass conversion to high-value products. Two approaches in biomass conversion that have succeeded in modifying the structure of lignocellulose to improve enzymatic deconstruction include thermochemical pretreatment and genetic modification. However, the characteristics of solubilized lignin resulting from different genotypes pretreated with different methods have not been extensively investigated.
Organosolv pretreatments, which employ an organic solvent to solubilize the lignin and hemicellulose components of biomass, have demonstrated the ability to both maximize sugar release for downstream processing to fuels and also to enable extraction of relatively high purity lignin suitable for making bioproducts. In this study, researchers compared three organosolv pretreatment systems—ethanol, tetrahydrofuran (THF), and γ-valerolactone (GVL)—on three switchgrass genotypes: wildtype (WT) and two transgenic switchgrasses genetically modified via down-regulation of the caffeic acid/5-hydroxyconiferyl aldehyde O-methyltransferase gene (referred to as COMT) and overexpression of the MYB4 gene (referred to as MYB). A fundamental understanding of the impacts of organic solvents and reaction conditions on the structure and properties of switchgrass lignin helps develop and optimize lignin-targeting organosolv pretreatments.
All organosolv pretreatments reduced the molecular mass of lignins, but to different degrees. THF-pretreated transgenic lignin retained the highest molecular mass, more β-O-4 linkages, and a higher aliphatic hydroxyl content than ethanol and GVL pretreated lignins. Ethanol pretreatment produced the greatest decrease in mass (∼90%) and near-complete removal of β-O-4 linkages. The abundant free phenolic hydroxide groups found in ethanol-pretreated lignin may make it suitable for development of antioxidant products, whereas GVL and THF lignins which retained more than half of their β-O-4 linkages may be more suitable for depolymerization to mono-aromatic compounds.
Detailed structural information about the extracted lignins was also provided by synchrotron small-angle X-ray scattering (SAXS) using the LiX beamline at the National Synchrotron Light Source II (NSLSII). The nanostructure observations revealed that ethanol pretreatment produced the smallest lignin particles from WT switchgrass. These analyses complemented insights from nuclear magnetic resonance and molecular dynamics simulations. A correlation was found between the molecular mass reduction of lignin molecules in the experiments and the number of hydrogen bonds between lignin and the organic solvents as calculated in the MD simulation, suggesting a connection between the depolymerization of lignin and its ability to form a hydrogen bond with the organic solvents.
Funding
This work is supported by DOE Office of Science, Biological and Environmental Research Genomic Science Program (ERKP752), and by the Center for Bioenergy Innovation (CBI) at Oak Ridge National Laboratory. The National Synchrotron Light Source II (for SAXS) is a U.S. Department of Energy (DOE) Office of Science User Facility operated for the DOE Office of Science by Brookhaven National Laboratory under Contract No. DE-SC0012704.
Related Links
References
Liang et al. 2022. Chemical and Morphological Structure of Transgenic Switchgrass Organosolv Lignin Extracted by Ethanol, Tetrahydrofuran, and γ-Valerolactone Pretreatments. ACS Sustainable Chemical Engineering, 10, 28, 9041-9052. [DOI: 10.1021/acssuschemeng.2c00948]